The future of converting is today. H.impress and Q.dura for improved service life.
The processes involved in tissue converting make a significant contribution to the end product’s key attributes – attributes customers might see as a sign of high quality. SchäferRolls presents new solutions for embossing back-up and marrying rolls which will improve the cover service life.
H.impress for the embossing process: Up to 15°C lower heat build-up
At high machine speeds, the tissue doesn’t have much time to be embossed while located in the roll nip. As a result, the embossing rolls don’t have much time to work their magic and achieve first-class embossing quality for the complete
tissue web. Add to that the increasing complexity of embossing patterns, with different depths of micro and macro embossing, and it’s clear that embossing back-up roll covers have their work cut out of them. To meet these high demands,
our embossing back-up roll covers are designed with particular attention to the wear, elasticity and resilience properties of the cover material.
With H.impress (fig. 1), SchäferRolls introduced a roll cover with excellent resilience properties and very low compression set. The low heat build-up and the increased mechanical resistance allow the machines to run reliably and according to plan while maintaining a consistently high embossing quality.
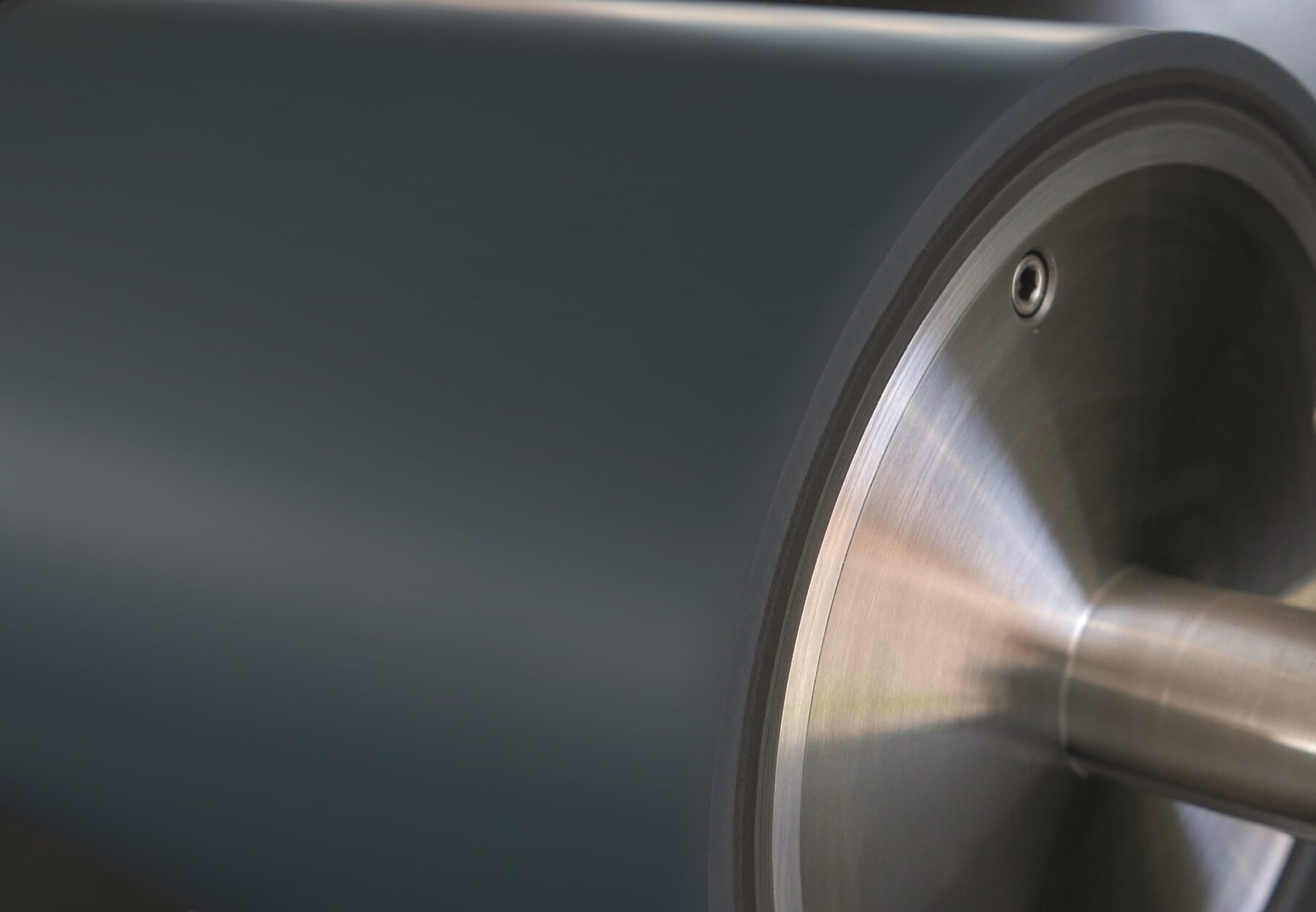
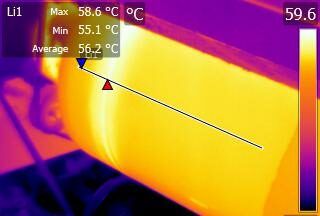
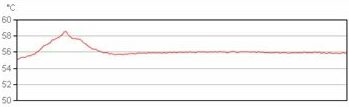
The important benefits of H.impress proved at Lucart S.p.A. in Diecimo, Italy: On line L216, the heat generation was much lower (56 °C) while the roll’s temperature profile remained stable (fig. 2) – compared to previously 70°C and frequent bearing failure due to uneven temperature distribution. These temperature results were confirmed also on line L220, where H.impress was able to reduce the heat generation for hysteresis by 10 to 15 °C lower than the best materials in operation until then. With cover H.impress, the customer had no more bearings failure on line L216 (four suffered in the year 2019) and no more cover delaminations on line L220.
Due to the good, reliable results, the new H.impress series has become a standard product in SchäferRolls’ portfolio for tissue converting lines and many customers successfully used this product on their lines.
Q.dura for marrying rolls: longer cleaning intervals
Ply lamination can be particularly challenging. Not only do the layers have to be glued together properly, the results should also look good without compromising the bulk tissue paper achieved during the embossing phase. This is
best achieved with narrow nips and short nip retention times. For easy handling, it is important that deposits of glue, dust or paper can be removed easily from the roll surface.
Q.dura (fig. 3) convinces with its dehesive, dirt-repellent surface and excellent cleaning properties, for example on the converting line of the producer Swedish Tissue from Kinda, Sweden, who previously suffered from extreme
glue build-up on the marrying roll cover from a competitor. Furthermore, the separation of threads from the cover, due to the bond of oil, dust and glue contaminated the paper (fig. 4). Changing to Q.dura improved the situation by
far: The cost-intensive and troublesome use of oil and scraper for cleaning became redundant, the cleaning intervals as such were increased while keeping a consistent high product quality.
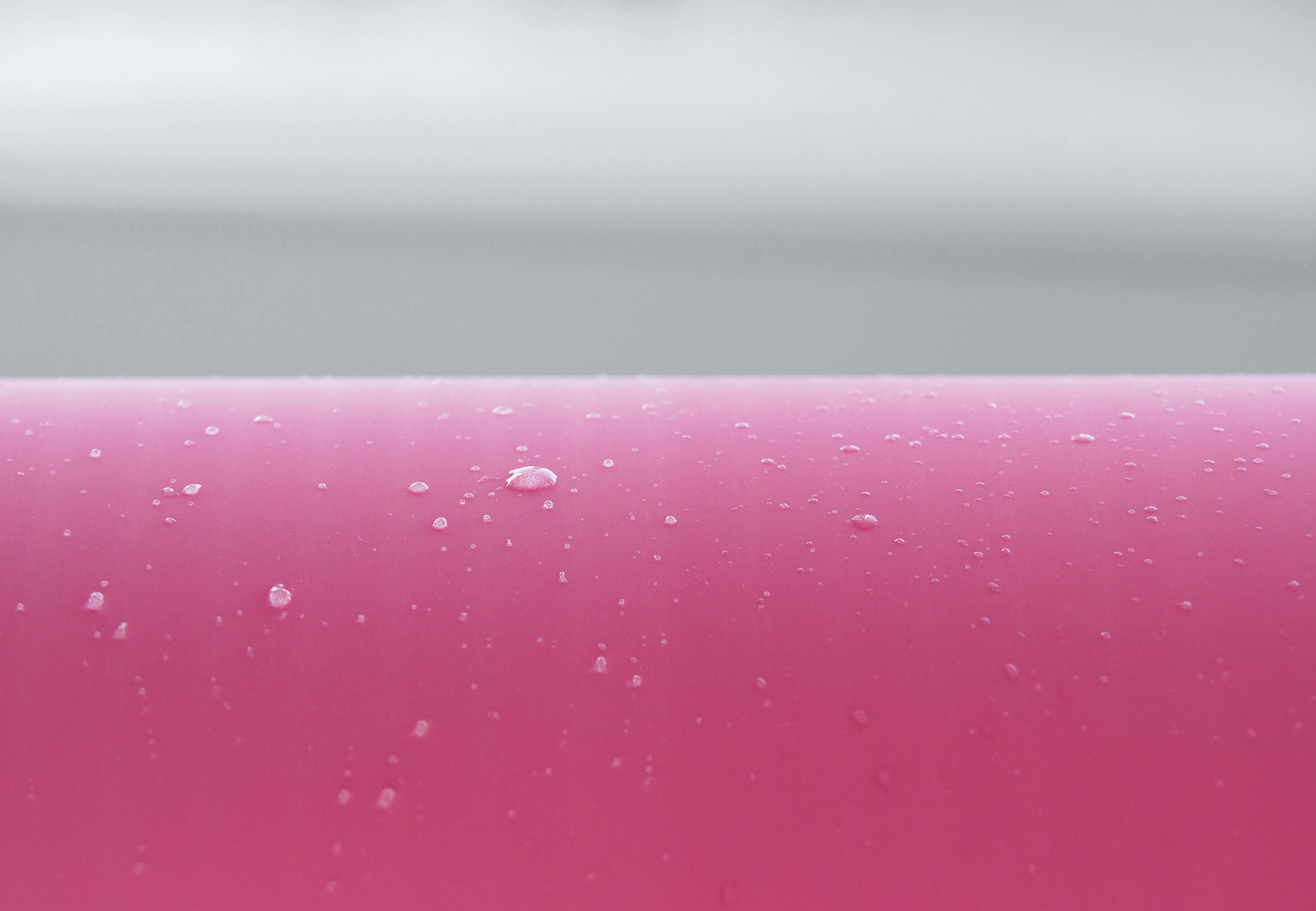
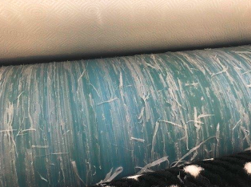
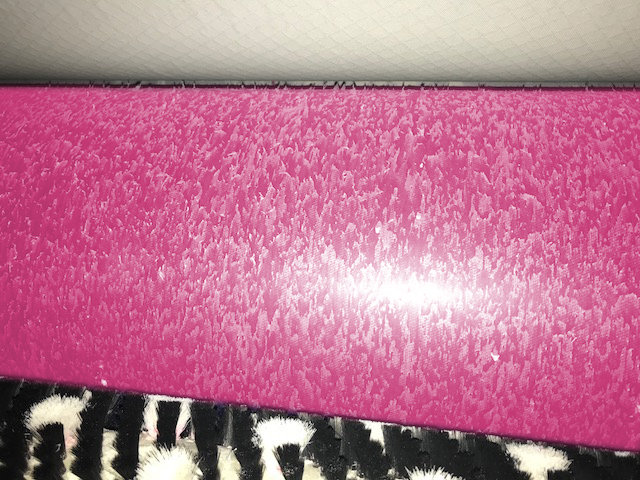
For applications using oil and a brush, glue deposits can be brushed off the roll surface effortlessly. With the right hardness setting, the cover ensures excellent ply bonding and high product quality in terms of bulk and softness. The outstanding abrasion resistance of the cover provides first-class runnability and an especially long service life.
Since the beginning of 2020, Q.dura has been the product of choice for customers looking for improvements in this position. Customer satisfaction is now reflected in more than 50 different positions with customers including OEMs.